The Top 10 Mistakes I Made in Building a Green Home
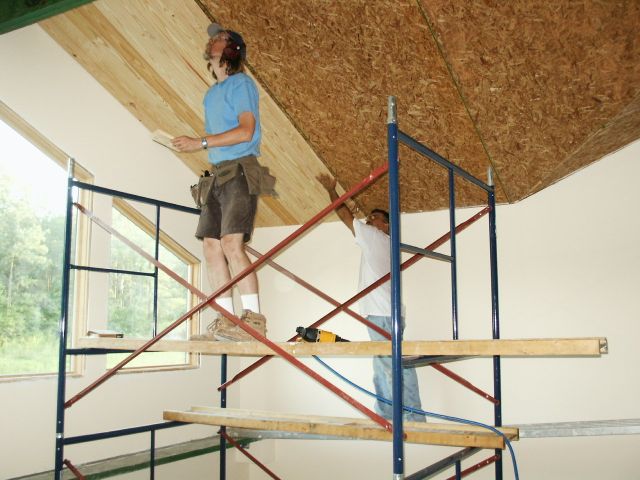
When I wrote about the net zero energy home that Amy Musser and Matt Vande built, I was really impressed that they were willing to share the mistakes they’d made and what they would do differently if they could go back and start over. Several readers remarked on that in the comments as well. Since I’ve puffed up my chest in this space several times and written about the green home I built a decade ago, I figure it’s about time for me to come clean, too.
Below are my top 10 mistakes, in roughly ascending order of importance.
10. Rented essential tools too long before realizing I really needed to own them.
Take that scaffolding you see me standing on above. I bought those three tables after having paid rent on a similar set for about six months. I could have saved money also by buying a storage container instead of renting one for 9 months. Same thing with a compressor and nail gun and reciprocating saw. Yes, I really was naive enough to think I could build a house without owning those essential tools!
9. Thought I could save money by doing more of the work myself.
In the very early stages, I had planned to do most of the work myself,† hiring help when I needed it. Having never built anything bigger than a bookshelf, I was clearly delusional. I did get a lot of great experience by doing so much of the work, but next time, I’ll make sure I have people who really know what they’re doing. At least I was smart enough to sub out the drywall, though!
8. Didn’t use an air gap behind the
fiber-cement siding.
I didn’t know much about air gaps back then, so we just nailed the HardiePlank lap siding directly to the walls. Also, I used #15 felt for the drainage plane and should have gone with #30. The fiber-cement siding will probably do fine for a long time; it may need painting more often, though.
7. Too much duct board and flex duct, not enough duct design.
We got a zoned system with plenums and short trunk lines made of duct board. The rest of it was flex duct. We didn’t have any hot or cold spots in the house, and I think the air flow, which I didn’t measure, was probably OK, but if the system had been sized properly (see #5), we might have had some distribution problems. The HVAC contractor did the duct design by coming over one Sunday with a notepad, walking the house, and deciding how he’d lay out the duct system. I don’t think he even used a ductulator to size the ducts, instead relying on his experience and rules of thumb.
6. Installed a water system without doing enough research.
We were trying to be as green as possible when we built the house, and it wasn’t an easy choice deciding whether to spend thousands of dollars to bring county water down to the house about 700′ off the dirt road that our 66 acres were on or thousands of dollars on a well. We went with the latter, then used a solar-powered pump. Rather than storing electricity to be able to pump on demand, we installed a 1500 gallon tank near the house and stored water instead. We ended up with iron bacteria in the water system and never really figured out a good retrofit solution. We went through a lot of filters.
5. Didn’t get an accurate Manual J load calculation.
I made sure that the HVAC contractor I hired did a Manual J load calculation to determine what size heating and cooling system we needed. He said we needed a 3 ton heat pump. Unfortunately, I didn’t know enough—or have enough time—to check his work and make sure it was right. A few years later, after my (now ex-) wife and I were already living in the house, I did a Manual J and found that the actual cooling load was only 1.5 to 2 tons. Lesson: Just because your contractor does a Manual J doesn’t mean that it’s correct.
4. Didn’t have our electrical plan completed before breaking ground.
If there’s one piece of advice I’d give you if you’re planning to build with structural insulated panels, it’s to have your electrical plan before getting anywhere near the point where you need it. The electrician is probably the trade most affected by SIPs, and I made the job even harder by not having this done. Fortunately, my electrician, Zot, is a friend and handled the job with great skill and patience.
3. Forgot to plan for basement insulation.
Oops. We changed from a crawl space to a basement to accommodate the composting toilet tank but didn’t think at all about insulating the basement walls. By the time I realized the mistake, we had HVAC, a composting toilet tank, electrical conduit and receptacles, and plumbing in the way. I did insulate and finish a room on the walkout side of the basement where most of the above-grade wall area was, but still, this was not smart at all.
2. Built too big a house.
The first sketch we made was about 400 square feet. Then it grew to 600, 800, 1100, 1500, and nearly 2000 square feet. At that point we added the full basement to bring it up to 3000 square feet. All those additional square feet seemed so important when we drew them in, but we realized later that we fell under the spell of the embiggening mind and just kept wanting biggerer and biggerer. (What do you mean?! Those are perfectly cromulent words!) Had we built smaller, we might have finished sooner, saved boatloads of money, been just as happy, and my ex-wife might not have had to sell the house in 2010—about the worst possible time to try to sell. An easy way to have had a house plenty large enough would have been to have the basement with only one floor above rather than two.
1. Didn’t spend nearly enough time in the design phase.
If I had it to do over again, this is the most important thing I’d do differently. If I’d spent 6 or 7 months designing instead of 4, we probably could have cut a year off of our construction time. The extra time might have solved all of the problems above and saved us a lot of money and heartache. We got ourselves into hurry-up mode because we were buying 66 acres with a construction loan and thought we needed everything to happen quickly. It didn’t. We should have paid heed to Albert Einstein, who once said, “If I had an hour to solve a problem, I’d spend 55 minutes thinking about the problem and 5 minutes thinking about solutions.”
After about 28 months of design and construction, we finally moved into the house in August 2003. It wasn’t a perfect house, but it was the most comfortable and efficient house I’ve ever lived in. Had I not made the mistakes above, it could have been even better. In my next one, I won’t make those mistakes; I’ll do my best to make all new mistakes instead.
Allison A. Bailes III, PhD is a speaker, writer, building science consultant, and the founder of Energy Vanguard in Decatur, Georgia. He has a doctorate in physics and is the author of a bestselling book on building science. He also writes the Energy Vanguard Blog. For more updates, you can follow Allison on LinkedIn and subscribe to Energy Vanguard’s weekly newsletter and YouTube channel.
Related Articles
How to Install a Branched-Drain Greywater System in a Green Home
Throwing the Building Science Learning Curve for a Loop
Working with Non-Green Trade Contractors in Building a Green Home
Footnote
† I have a history of thinking this way. In 1983, right after graduating from college, I bought a book called Backcountry Bikepacking and starting planning a solo bike trip. My imagination ran away with me, and soon my route had me riding from Shreveport, Louisiana to western Pennsylvania, then across the top of the Great Lakes, and finally down to St. Louis…just in time to start grad school at Washington University two and a half months later. By the time the trip started, I’d pared it down to a relatively modest 630 miles from Shreveport straight to St. Louis. The saner trip took 12 days of riding.
This Post Has 8 Comments
Comments are closed.
You said “… if the
You said “… if the (HVAC) system had been sized properly, we might have had some distribution problems..”.
I submit that oversizing does nothing to alleviate distribution problems. It may even aggravate them.
The fact you are not complaining about distribution problems, hints the duct design might be adequate. You are in a heating dominated climate and the need for humidity removal in summer is probably minimal. One of the big knocks on oversizing is AC short cycles and discomfort due to high humidity because the AC needs long-ish cycles with the coil equilibrated below the air dew point. The first few minutes are ineffective at humidity removal, and right-sizing is the best way to get long run times.
My understanding is you might have *some* discomfort from short cycles of heavy heating/cooling, but the major efficiency pitfalls are probably not hurting you much. Congratulations on what you did right.
I found it interesting that
I found it interesting that the #1 ISSUE you named was DESIGN. I guess the old adage of “An ounce of planning is worth a ton of fixing” sees to be lost on most. I always wonder why the aversion of hiring a good architect?
All in all your house sounds much better then 90% of US homes from that time.
My wife thought she was
My wife thought she was getting the good end of the deal when we agreed that she would do all the planning, and I would do all the work. B-b-b-a-a-a-w-w-w-a-a-a-a-h-h-h-a-a-a ! Marriage intact none the less.
The part about taking time
The part about taking time with design, guess it’s hard to overemphasize that one. On the other hand there is something to be said for those who can implement.
Allison, your posts are STILL getting better! Sharing your “I’d do over’s” is a great public service. Nice work.
Anyone who builds their own
Anyone who builds their own green home with their own two hands is going to have a long list of mistakes in the end.
Those who have their house built for them will have that same list of mistakes – except it’ll be in the drawer of the desk of the contractor and/or architect they hired.
Many times while building our green home (off grid, straw bale) I wished for that big “do-over” button. I never found it. Lessons learned and now I’ve become a bit more humble as I look back on my mistakes. There is no going back so why beat yourself up.
Some of whats listed above is site specific. Design is not and I cannot stress the importance of that one enough. Design for a year (no make that two) and have more than a few people look over your final plan. Once you have your final design, crumble it up and start again. Make a few more designs and be open to suggestions from others. Finally it’s time to sit down and draft your working plans. If your using an architect and he designs something you approve, smack him in the face, fire him and get an new architect. Fire that one too. If you’re building it yourself, draw it yourself so you understand fully what to do. Try not to second guess your plans a year into the build. Source all your materials long before you break ground. Horde as much money as possible then get a loan – double the amount. If you have the slightest doubt about your abilities or those you intend to hire to help, think twice before taking the plunge.
The “Seven P’s”
Hello,
Hello,
The best part of your mistake is your design. I love that and generally seen this type of mistakes with other people. Thanks for sharing your thoughts with us.
Very good article. Maybe I’ll
Very good article. Maybe I’ll write a sequal. Just finished my own LEED Silver home and think you have a great list. I spent a great amount of time on my plans and did a gut & rehab. To add to the list,item #11, I would say keep all your ductwork within your interior envelope. I ran ductwork over a barrel on 1/2 of the second floor and did not realize the cuts I made to bring the supply and returns down the walls created big air leakage voids to the attic. Also, I worry that I loose too much heat or cooling. Leak gaps are fixed, but not a good HVAC design move.
#12 is preplan you arc fault beakers and pull seperate neutrals (I didn’t and it was messy to meet NEC code).
We have come along way since
We have come along way since the 1950s.Some good and some bad. My father was a house builder after WW2 and I thought that was the way I going to work.I decided to work in the auto field as a mechanic and living through the great 60s and lousy 70s went back to school for HVACR.Thanks to a great job and after working for many companys I learned what my father said about to tight of housing and not to go to far with the seal up.Knowing in my present house of 1300sqft.and fairly well insulated I do not have problems with mold or stall air.Being my wife has CF I had to shut down the humidifier and a least weekly turn on 3 exhaust fans and suck out the bad air and bring in the good as long as my neighbor isn’t burning wood uncontrolled I get a good air change.My theory is do not build to big of a house and try to seal it to save $100.00 a month on your heating bill.My wife has much less problems with her CF after doing these simple things.All exhaust fans dump to the out side.Fresh air comes from outside with no contaminated air( neighbors wood stove).I do not want to live in a vacuum bottle.Adding a little outside air into your HVAC system through a heat transfer unit will pressurize your home abov outside pressure to let fresh air in.I would spend the extra to have a safe breathing house.As we all know by now everything in your house gives off something we breathe