Ventilating High-Rise Multifamily Buildings — A First Look
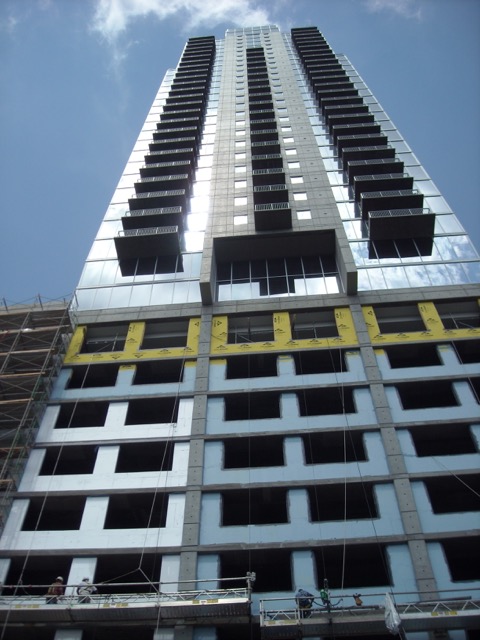
Condominiums and apartments present some serious challenges when it comes to providing ventilation for good indoor air quality. (I live in a condo that was built in 1970 with no whole-house mechanical ventilation, but that’s another story.) In high-rise buildings, wind and stack effect often render mechanical ventilation strategies useless, especially for the lower parts of the building. Let’s take a look.
Theory and practice of high-rise ventilation
Lorne Ricketts of RDH, an engineering firm, gave a talk at Building Science Summer Camp last year about ventilating high-rise buildings. He began with a case study of a 13-story residential building in Vancouver. The ventilation strategy in this building was to use a big blower on the rooftop to heat or cool outdoor air and blow it down into the corridors of all 13 stories. The image below is from his presentation, which you can download from the Building Science Corporation website (pdf).
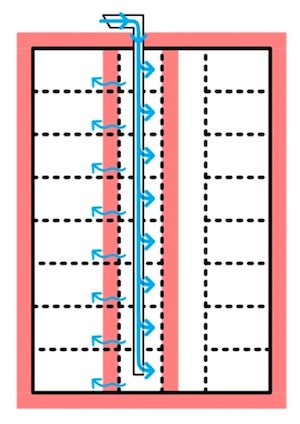
Once the ventilation air is in the corridors, theory pushes it into the dwelling units through the intentional entry door undercuts. You can see those little arrows sliding under the doors in the drawing above, so it must be true. Right?
Well, not really. There’s an old saying: “In theory, there is no difference between practice and theory. In practice, there is.” (I used to tell people this quote is from Yogi Berra, but Snopes has cast doubt on that attribution.) So all those nice arrows showing a uniform distribution of ventilation air don’t really match the practice. Here’s why.
First, air moves from one place to another because of two things: a pressure difference and a pathway. The door undercuts provide the pathway, but the pressure differences vary. The mechanical ventilation system isn’t the only mechanism for creating pressure differences. Ricketts showed the diagram below summing up the contributions of wind, stack effect, and the mechanical system.
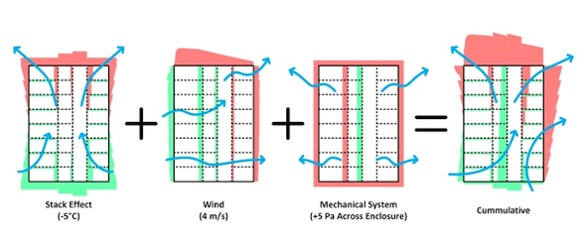
But the driving forces aren’t the only problems. The pathways are, too. A lot of that ventilation air doesn’t make it into the corridors because of leakage to elevator shafts and other places. Their measurements showed only 40% of all the ventilation air actually made it into the corridors. Wow!
Then they measured how much of that air got into the dwelling units via the door undercuts. The result: only 20%. Whoa!
Then they did the math: 40% x 20% = 8%. What?!
Vancouver, we have a problem! (It’s OK. I can say that because I’m from Houston.)
The ventilation disparity
As you can see, the net result is that the units on the upper floors get a lot more ventilation air than the ones on the lower floors. In fact, their tracer gas testing showed there was an order of magnitude (10x) difference in the ventilation rates from bottom to top. They to about 10 cubic feet per minute (cfm) at the bottom and nearly 200 cfm at the top.
As a result, the lower floors have more indoor air quality problems than the upper floors. The levels of carbon dioxide were higher. There was more infiltration from the garage at the bottom of the building.
Clearly, the pressurized corridor ventilation system didn’t work for this building. They looked at the driving forces (wind, stack effect, mechanical) in buildings of other heights and in other climates. They concluded that mechanical systems couldn’t “overwhelm nature” and that corridor pressurization wasn’t a good ventilation strategy.
The plan for improvement
Based on what they found, the team proposed this:
- Do lots of air sealing between the garage and living spaces
- Compartmentalize the dwelling units to reduce air leakage among units
- Install a heat recovery ventilator in each dwelling unit
- Install a smaller rooftop ventilation unit that ventilates only the corridors
That’s a system that can work in both theory and practice!
Download Lorne Ricketts’s presentation: Ventilation in Multi-Family Buildings (pdf)
Related Articles
An Energy Recovery Ventilator Is NOT a Dehumidifier
Adventures in Hotel Bathroom Ventilation
4 Ventilation Quotes That Will Rock Your IAQ World
Image credits: High-rise condo building by Energy Vanguard; two ventilation drawings from Lorne Ricketts’s presentation
NOTE: Comments are moderated. Your comment will not appear below until approved.
This Post Has 5 Comments
Comments are closed.
Would compartmentalizing each
Would compartmentalizing each unit mean door sweeps would be needed to compensate for the undercut doors? I think the answer us yes but just making sure…
Yes, Jason, each unit would
Yes, Jason, each unit would be isolated from other units and common areas.
Another fine analysis,
Another fine analysis, Allison.
While I have nothing to add to your article, I thought an anecdote from days gone by might be of interest. In another life, I worked in Technical Services for PEPCO in DC and one of my duties was to visit with our commercial customers who requested assistance in understanding our rate structures. I also regularly visited sites for a “walk through” to provide a second set of eyes and perhaps identify low hanging energy fruit that had escaped notice of the building engineer. A particularly memorable visit was to a venerable, multi-storey apartment structure on Massachusetts Ave. in the city that had been built well before the era of mechanical cooling systems.
While walking a hallway with the building engineer, I inquired about the grated, and now enclosed, transoms above each apartment door and he said, “You have got to see this”. Deep in the basement he showed me an ancient fan, that we were able to step into and I marveled at the size, which had to be over 10′ in diameter. A duct system connected the 75hp air mover to all hallways and when operated, depressurization drew air through apartment windows and out the transoms. While doing nothing to mitigate brutal summer DC humidity, I’m sure the air movement provided a welcome, modicum (small “m”) of relief to the beleaguered tenants.
So I looked at the New
So I looked at the New Zehnder ERV, and its intake and exhaust are on top of each other in the same pipe, leading to its outside intake and exhaust being on top of each other. Shouldn’t the exhaust and supply be separated by something like a 6′ minimum?
Donald, I asked John Rockwell
Donald, I asked John Rockwell at Zehnder about that and he said a couple of things. First, the grille you see on the Zehnder page isn’t the one they’re using now. They’ve changed to one that has intake and exhaust on the left and right sides of the outdoor termination. Second, they’ve done testing on cross contamination and found that it’s “comparable to or better than” a system with intake and exhaust outlets separated by 6 feet. I’ll be writing more about this system so stay tuned.